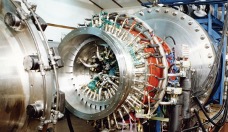
The VKI compression tube CT-3 is a world-class rig for testing turbine hardware of modern gas turbine engines for aircraft propulsion and power generation.
The CT-3 test vehicle is a transient blow-down facility operating on the principle of the isentropic light piston compression tube. The wind tunnel consists of three main elements: the compression tube, the test section and the dump tank. The upstream cylinder (8 m long with a diameter of 1.6 m) contains a free-moving light piston driven by high-pressure air supplied by 6 vessels at 300 bars. The test section that contains the research turbine is located in between the two reservoirs. A fast-opening shutter valve separates the compression cylinder from the test section which is connected to the vacuum tank via an adjustable sonic throat.
The compression tube can deliver stage massflows between 5 and 20 kg/s with running times at steady state conditions of the order of 0.5 s. The turbine Reynolds and Mach numbers can be independently adjusted over a wide range. The rotor can spin up to 8,000 rpm and generate instantaneous powers of 1-2 MW with the acceleration of the rotating parts limited by an inertia wheel.
The intermittent operation of the rig allows for accurate measurements of convective heat transfer on vanes, blades and endwalls at engine-like gas-to-wall and gas-to-coolant temperature ratios.
With an outer diameter of nearly 1 meter and blade heights up to 100 mm, the VKI CT-3 is one of the world’s largest short-duration turbine facilities. The test section hosts a rotating turbine stage and there is room to install a second stator downstream connected through an aggressive s-shaped duct. The rig is also equipped with an independent supply system that can use air or a foreign gas to deliver coolant to stator and rotor airfoils and platforms as well as disc cavities.
The turbine hardware is evaluated using fast-response instrumentation that measures unsteady heat flux (thin-film gauges) and pressures (piezo-resistive pressure sensors) on airfoils and endwall surfaces, miniaturized directional probes, hot-wire anemometers, thermocouples rakes, and unsteady gas temperature probes that survey the inlet and outlet flow conditions, measurements of stage mass-flow, and shaft torque to determine turbine efficiency, single-blade tip clearance by high-bandwidth capacitive probes. The test section is also equipped with windows on the rotor shroud to access the rotating hardware for application of particle-image-velocimetry and other optical techniques. A 16-contact infrared opto-electronic data transmission system permits high-frequency measurements on the rotating parts.
The wind tunnel is used to investigate the aerodynamics, heat transfer and efficiency of cooled high-pressure turbines, rim-seal and cavity flows, leakage flows and unsteady blade row interactions. Rainbow rotor and stator rows can be used to measure simultaneously the aerothermal flows of different digitally optimized turbine designs. In a recent upgrade, the test section has been adapted to study a high-speed low-pressure turbine representative of those to be found in next-generation geared turbofan engines
Reynolds range : 200,000 – 1,500,000
Mach range : 0.6 – 1.3
Max temperature : 500 K
Max pressure : 2.5 bars
Max rotating speed : 8,000 rpm
Measurement instruments2 On wall and traversing pneumatic pressure probes (total, static, directional).
Hot wire anemometry. Fast response pressure probes. Thermocouples. Wall
heat flux thin films. Flow visualization.
Comment
PropComb Variable Mach (low subsonic to supersonic) and Reynolds (take-off to cruise) number
1 ½ turbine stage. Aero-thermal performance determination, rotor/stator and
rotor/rotor interaction (possibly time resolved). Aero-engine similarity conditions,
including film cooling. Short duration facility (< 1 sec).
Instrumentation
Fast-response surface piezo-resistive pressure sensors, surface thin-film heat transfer gauges, miniaturized multi-hole pneumatic/ fast-response directional probes, thermocouple gas temperature probes, fast-response flow temperature probes, hot-wire anemometry, cold-wire thermometry, fast probe traversing systems, PSP, time-resolved PIV, blade-resolved capacitive tip clearance sensors
Sergio Lavagnoli – Professor in turbomachinery and Propulsion Department