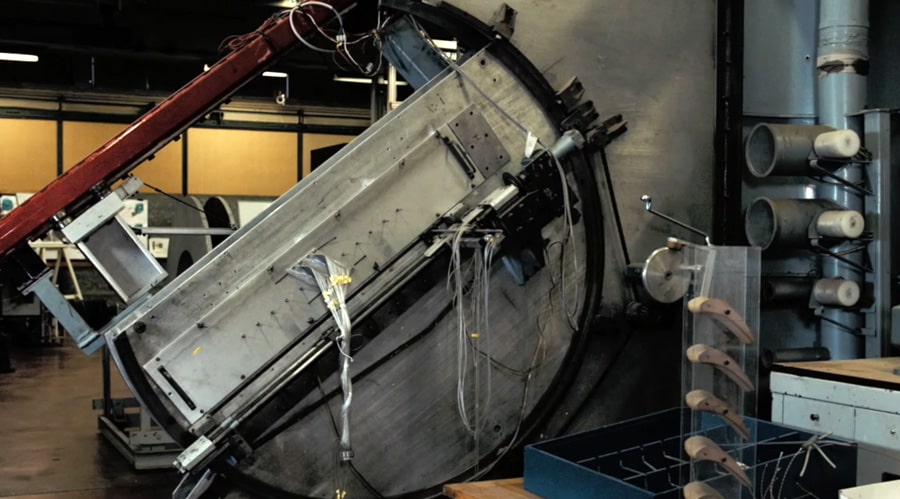
The C-1 facility is a continuous-flow, low-subsonic rig that is designed and used for development of axial blade profiles and investigations of primary and secondary flows in compressor and turbine cascades.
The rig has a non-return arrangement with atmospheric intake and exhaust through a rectangular test section. The air is supplied by a centrifugal blower driven by a DC motor. The flow enters a settling chamber through a diffuser and three mesh screens. The flow is then ducted to the cascade inlet though a convergent nozzle.
The inlet test section area is rectangular with a height of 127 mm and a width of 500 mm. The test section can typically fit up to 15 blades with relatively high aspect ratio (2-4). The cascade is mounted on a rotating support that allows easy modification of the inlet flow incidence.
The rig is equipped with slots at the side walls that can be used to remove the boundary layer upstream of the test section. An auxiliary exhauster driven by a DC motor is used for boundary layer suction independently regulated at each slot by dedicated valves.
The Reynolds number can be adjusted to simulate realistic engine conditions between 50,000 and 250,000 based on an airfoil chord of 50 mm and exit velocity. Maximum Mach numbers are in the order of 0.10.
The cascade test section can be densely instrumented with a combination of traversable probes (multi-wire anemometers, miniaturized directional / total pressure probes), surface sensors (hot-films and pressure taps) and optical techniques (time-resolved PIV and LDV) to characterize the inlet flow, the status of the blade boundary layer, the airfoil wakes and the secondary flow evolution through the passage.
Reynolds range 30,000 – 500,000 (variable airfoil chords)
Mach range < 0.15
Max temperature 300 K
Max pressure 20 mbar (dynamic pressure)
Max rotating speed NA
Instrumentation
The cascade test section can be densely instrumented with a combination of traversable probes (multi-wire anemometers, miniaturized directional / total pressure probes), surface sensors (hot-films and pressure taps) and optical techniques (time-resolved PIV and LDV) to characterize the inlet flow, the status of the blade boundary layer, the airfoil wakes and the secondary flow evolution through the passage.
Sergio Lavagnoli – Professor in turbomachinery and Propulsion Department
sergio.lavagnoli@vki.ac.be